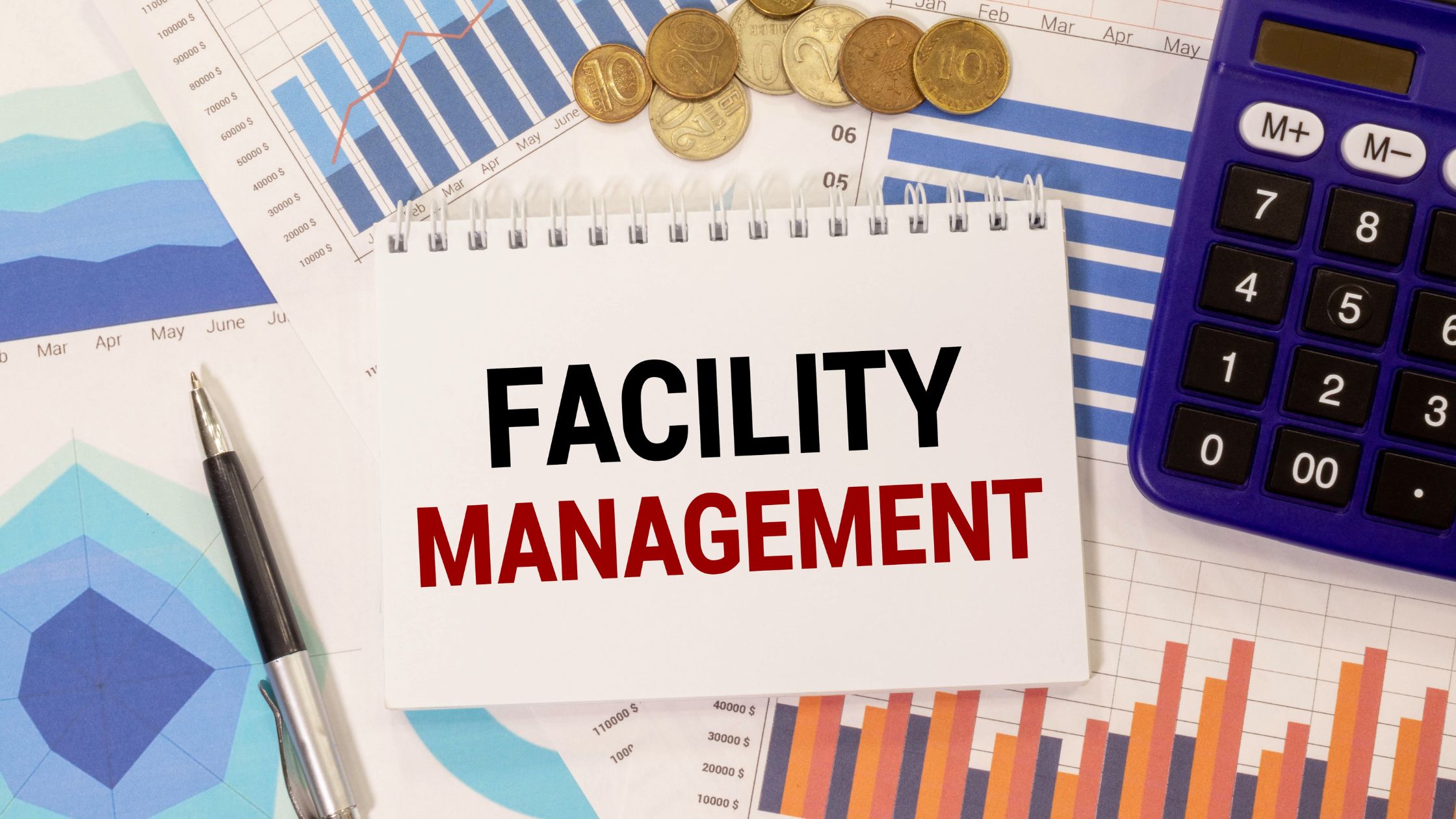
The Role of Facility Management in Modern Businesses
As an organization grows, every aspect of it needs to be safe, efficient and cost-effective. The way it operates must be optimal to flourish in its business segment. Facility management is critical in ensuring that operations are streamlined across industry facilities. The facilities in the retail stores, manufacturing plants and warehouses must be managed effectively. Only then can these facilities be considered safe, functional, and productive environments for technicians and customers.
Why Facility Management Matters
Facility management extends beyond keeping the lights on and floors clean. It includes a vast range of responsibilities that influence a business to be successful. Here’s why:
Operational efficiency: Preventive maintenance helps ensure that your facility is properly maintained and that production downtime is minimised and workflows are efficient and smooth, ultimately boosting business productivity overall.
Cost savings – CMMS enable proactive maintenance of machines so that expensive equipment failures and repairs can be avoided. Moreover maximum utilization of energy can also save a lot on utility bills.
Safety & well-being: A clean, well-managed, and compliant work environment promotes employee well-being and reduces the chance of accidents and occupational illnesses.
Builds Positive Image – A well-maintained facility helps in leaving a good impression on clients, guests, and investors thereby helping developing improving brand image.
Facilitates Business Expansion: With growth, a business needs the space to cater to that demand so that the facility management secures the growth by designing and managing relocations to efficiently optimize the existing space or the redistributed space.
Â
Industrywise Facility Management Challenges
Although the basic principles of facility management are the same across industries, challenges are industry-specific. A Deeper Dive into Verticals and Their Most Pressing Pain Points:
Retail:
Heavy Traffic and Natural Wear & Tear: Periodic high customer traffic tends to cause equipment to need more frequent cleaning, and to limit the ability to place units out of service for technical maintenance.
Regulatory Compliance and Food Safety: Food storage, handling and sanitation are closely regulated and recorded, requiring comprehensive upkeep of proper documentation.
Manufacturing:
Production uptime is essential – Equipment failures can demean your production past the point of no return and generally result in huge budgetary issues. This makes the need for predictive maintenance critical.
Safety is a top concern: Manufacturing facilities work with dangerous compounds and processes that need stringent safety protocols in addition to regulatory compliance.
Warehousing:
Managing Large Spaces: Warehouses have a lot of space they occupy, this makes it difficult to be able to monitor equipment, perform uniform maintenance activities, and put their spaces into maximum use.
Inventory Management: Guaranteeing seamless flow of goods calls for proper working tools and availability of spare parts that will reduce time wasted.
Â
How Nexcilo CMMS Can Help
These facility management challenges can easily be addressed by the application of Nexcilo CMMS in businesses across various industries. Here’s how Nexcilo makes facility management more powerful:
Centralized Data Management: Nexcilo produces a hub for all facility information, including equipment details, repair histories and space layouts. This information is easy to access and interpret hence facilitating sound decision making.
Preventive Maintenance: Using Nexcilo scheduling and tracking preventive maintenance tasks becomes easier thus ensuring that equipments are serviced on time. Avoid breakdowns and prolong the lifespan of equipment that was otherwise not possible.
Work Order Management: With the help of Nexcilo simplify creation, assignment, and tracking of every work order. Allow technicians to access work order details as well as equipment history remotely. Enhance prompt responses at any given time as well as efficient repairs.
Inventory Control: With Nexcilo, get access to the real-time data based on various stock levels at different sites helping in managing the spare parts inventory precisely. This enables ordering ahead of time and reduces the likelihood of stockouts during maintenance activities.
Compliance Management: For specific compliance requirements in some areas such as cleaning schedules, Nexcilo helps with planning and overseeing those arrangements. It records these tasks’ completion rates through report generation so as to meet regulatory conditions.
Cost Optimization: Nexcilo helps prevent equipment failures, streamline maintenance processes and optimize energy usage. With such advantages businesses can reduce operational costs, attain financial stability and focus more on innovations for the future.
Â
Customized Solutions with Nexcilo
Our Nexcilo CMMS is a system flexible enough to adapt to the individual features of every industry. Some examples include:
- Retail: With Nexcilo easily generate checklists for task and food safety protocols which in turn helps in ensuring compliance and a safe environment. In addition, it can be scheduled for preventive maintenance services on high-traffic pieces of equipment such as coolers and registers, so that such work done during peak hours could minimize inconvenience.
- Manufacturing:  Conversely, avoid equipment failures with Nexcilo’s preventive maintenance so as to connect with machine sensors for predicting problems even before they happen. It also keeps track of health and safety certifications that are required by different personnel. This becomes very useful in the case where government regulations need to be adhered to.
- Warehousing: Nexcilo offers space management functions that helps optimize warehouse layouts improving storage efficiency as well as retrieval of goods. It also provides details about where pieces of equipment are located at any given time within the vast warehouse facility.
Â
Conclusion
Nexcilo offers solutions for all industries that perform facility maintenance, which can be customized according to specific needs. The deployment of our software into your facility will immediately reflect in the performance and the financial returns of your operations. To know more visit www.nexcilo.com