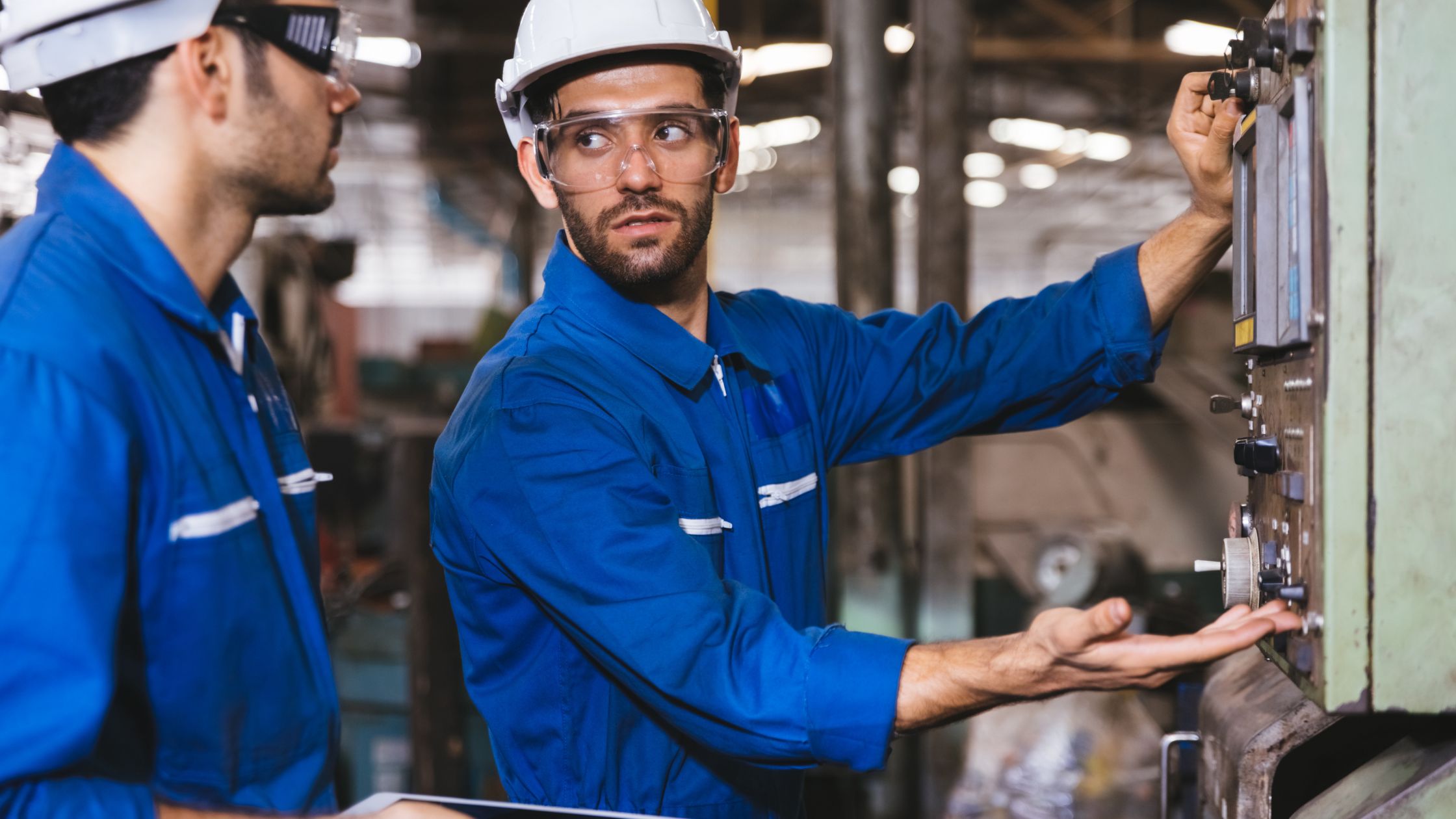
How CMMS Can Solve Modern Day Maintenance Challenges
Tackling the Modern Maintenance Maze
It is technology that drives today’s business forward. And there is no doubt that businesses should leverage it to their advantage. Maintenance teams in organizations too can use technology driven solutions to stay ahead of the challenges. They face challenges capable of hindering organizational productivity and profitability. From unexpected equipment breakdowns and extensive maintenance backlogs to missing parts and escalating costs, the list never ends. As organizations try staying competitive in the business sphere the need for efficient maintenance management becomes more critical than ever. This is where CMMS comes in to rescue from the maintenance troubles.
A Computerized Maintenance Management System (CMMS) software helps in centralizing maintenance data to facilitate the processes associated with maintenance operations. Nowadays CMMS is a necessary tool for organizations across sectors. Retail, Warehouse, and commercial services all use CMMS to navigate the difficulties of modern maintenance.
7 Features to Solve ModernDay Maintenance Challenges
- Work Order Management
One of the most significant advantages of CMMS is its ability to streamline work order management. Create, assign, and track digital work orders with ease. Key features of CMMS work order management include:
- Paperless Work Orders: Eliminates paperwork with real-time work order creation, assigning and tracking.
- Work Request Portal: Allows non-maintenance staff to submit maintenance requests and track their status.
- Instructions and Documents: Provides technicians with access to task lists, manuals, and other relevant documents.
- Tracking: Monitors the status and costs of work orders.
Challenges Solved: Increases visibility and traceability of maintenance process, reduces downtime, improves efficiency of management, streamlines workflows and ensures access to essential information for technicians.
- Scheduled Maintenance Planning
CMMS addresses downtime and costs in organizations with preventive maintenance programs. The scheduled maintenance planner within a CMMS allows for:
- Trigger tasks: Initiates maintenance tasks based on time, usage, condition, or events.
- Calendar Views: Provides an overview of maintenance schedules and workloads.
- Maintenance Forecasting: Aligns upcoming tasks with inventory purchases and work schedules.
- Inspection Checklists: Attaches detailed inspection tasks with pass/fail guidelines.
Challenges Solved: Prevents reactive maintenance by helping transition to preventive maintenance, optimizes maintenance schedule frequency, and reduces overspending.
- Parts and Inventory
Proper inventory management is critical in various organizations. CMMS facilitates inventory control through features such as:
- Parts and Safety Equipment: Lists the exact numbers of spare parts and safety equipment.
- Parts Monitoring: Tracks inventory levels, locations, and costs.
- Low Stock Alerts: Sets minimum quantities and automates reordering processes.
- Multi-site Organization: Manages inventory across multiple facilities.
Challenges Solved: Prevents maintenance delays caused by inventory shortages, reduces costs by avoiding overstocking, and improves inventory management efficiency.
- Comprehensive Asset Records
Maintaining accurate asset records is crucial for effective maintenance management. CMMS provides digital asset profiles that include:
- Asset Hierarchy and Location: Organizes assets and tracks their locations.
- Repair History: Logs past issues and resolutions for each asset.
- Financial Tracking: Records labor and part costs associated with each asset.
- Documents and Notes: Attaches manuals, diagrams, and safety notes to assets.
- Vendor Information: Stores warranty and vendor contact details.
Challenges Solved: Facilitates better asset management, facilitates quick access to essential information, ensures compliance, eases audit preparations and enhances decision-making.
- Precise Maintenance Analytics
Data-driven decision-making is at the heart of modern maintenance practices. CMMS offers robust maintenance analytics through centralized dashboards, enabling continuous performance monitoring and progress evaluation. The key benefits include:
- Performance Monitoring: Ensures optimal functioning of operations by keeping track of ongoing performance metrics
- Enhanced Communication: Ensures seamless interaction with all stakeholders involved to promote clarity.
- Growth Assessment: Measures the improvements and advancement in the maintenance practices.
Challenges Solved:Â Improves performance visibility, bridges communication gaps, and eases process failure analysis. Also helps identify areas needing improvement with KPI analysis and enhances asset longevity.
- Mobile Access
We live in a period where mobility is key, and CMMS is the answer. Enable maintenance teams to access information and perform tasks on the go. Features of a mobile CMMS app include:
- Fast asset info: Instantly retrieve asset information by scanning codes.
- Push Notifications: Receive alerts for new work orders and task assignments.
- Offline Access: Record data even without an internet connection.
- Photos and Voice-to-Text: Attach photos and voice notes to work orders.
Challenges Solved: Enhances accessibility of maintenance teams. Enables faster issue redressal and enhances collaboration regardless of location.
- Simplified Reporting and Compliance
Generating reports and ensuring compliance with regulatory standards can be time-consuming. CMMS simplifies these processes with one-click reporting capabilities, including:
- Pre-built and Custom Reports: Select from pre-built templates or create custom reports.
- Dashboard Reports: Access real-time maintenance metrics on the CMMS dashboard.
- Scheduled Reports: Automate regular reporting to keep stakeholders informed.
Challenges Solved: Provides actionable insights, saves time, and facilitates data-driven decision-making. Identify problems and ensure compliance with industry standards and regulations.
Conclusion
In the modern age maintenance challenges need modern solutions. A CMMS offers a complete toolkit to tackle all the maintenance issues. From work orders to data analytics CMMS empowers organizations to achieve efficiency, reliability, and cost-effectiveness.
Adopting a robust CMMS is a game-changer for companies facing management barriers. Be it organizations, facility management companies, commercial service contractors or any other firm. CMMS solves immediate maintenance challenges and paves the way for a resilient and bright future for businesses.
Ready to take your maintenance operations to the next level? Discover the next-level CMMS solution Nexilo transforms your maintenance management. Let us help you overcome modern-day challenges with ease. Contact us today to learn more and get started on your journey toward maintenance excellence.